Quality System Development
Quality Management System (QMS) challenges are not limited to start-ups. Using EMMA International’s proprietary methodology, we’ll help you implement a quality management system that is Compliant, Lean, Integrated, and Customizable (CLIC™).
Our CLIC™ methodology is proven to be sustainable, easy to follow, scalable, and cost-efficient. CLIC™ can be tailored to your business needs and scaled to your size of the operation. It also requires minimal resources for you to maintain ongoing compliance while developing safe, effective products.
For specialized industries such as digital health, CLIC™ integrates with internationally recognized IEC 62304. For contract manufacturing operations with automotive manufacturing abilities, CLIC™ can be integrated with IATF 16949.
A CLIC™ QMS fully supports GMPs, GDPs, GCPs, and GLPs across all life-sciences industries.
We customize CLIC™ to comply with the regulatory requirements for your target market. View a selection of some of the regulatory requirements we cover.
Medical Device
Compliance Options:
- 21 CFR 820
- 21 CFR 801
- 21 CFR 803
- 21 CFR Part 11
- ISO 13485
- ISO 14971
- IEC 62304
- EU MDR/IVDR
Biologics
Compliance Options:
- 21 CFR 600
- ISO 9001
Combination Products
Compliance Options:
- 21 CFR 210
- 21 CFR 211
- 21 CFR 820
- 21 CFR 803
- 21 CFR Part 11
- ISO 13485
- ISO 14971
- IEC 62304
- EU MDR/IVDR
Don’t see your regulatory requirement? Contact our technical team.
A CLIC™ QMS provides an optimized workflow for each of the following QMS processes:
Validation
We have the expertise to provide effective design and process validations. Notably, we provide a complete validation process implementation including a unique, customized Validation Master Plan. We develop individual validation plans, conduct validations, and write the final validation reports and supporting documentation.
Quality Audits
We’ll optimize your audit process, train your auditors, and help you adhere to your audit schedule. Additionally, we provide complete independent audits for all functions and requirements. We provide effective audits to all ISO, EU, QSR, CMDR, GMP, GLP, and/or GCP standards and requirements. A final report will be provided that not only meets your regulatory requirements, but also identifies your systemic quality problems.
Design Controls
We will work with your R&D staff to develop practical and effective design requirements, validations, and Device Master Records (DMR) as required by the FDA. We will help you produce safe and effective products through implementation
Supplier Quality
Protect your business and your stakeholders. EMMA International performs supplier audits at a reasonable cost. Fulfill this regulatory requirement and gain valuable information concerning the quality and reliability of your suppliers and their products. Our experts will also implement supplier qualification and approval/disapproval processes, including a supplier assessment process.
Digital Health
EMMA International’s integrated QMS ensures that your software development lifecycle and its maintenance align with the internationally recognized IEC 62304 to give you an added competitive advantage. We support your development process from start to finish, and even reverse-engineer your software product to create Software QA documentation as part of remediation.
Ready to design a QMS that CLICs? Contact one of our experts.
Ready to learn more about working with us?
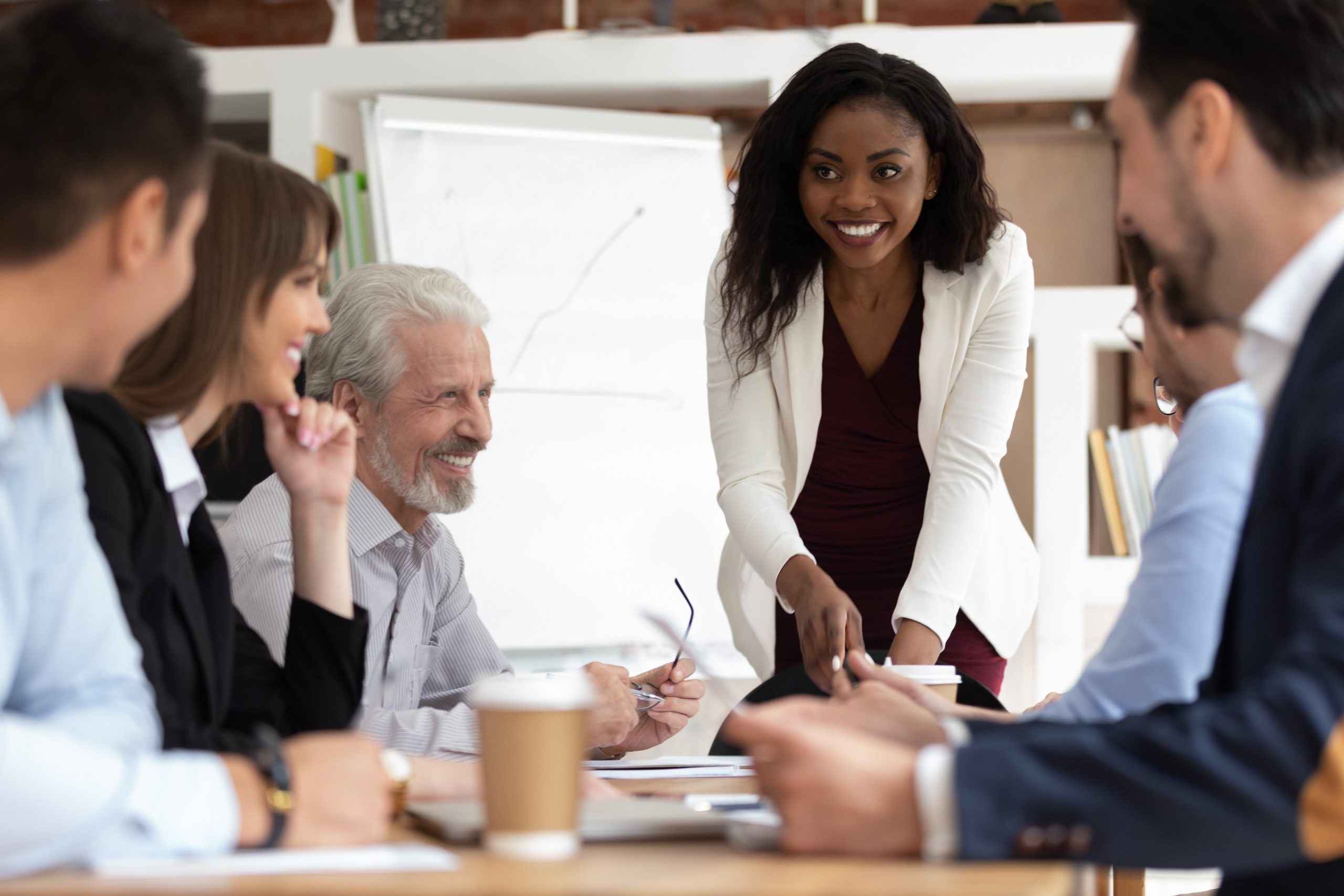
Quality System Resources
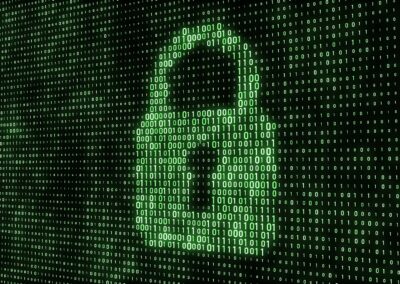
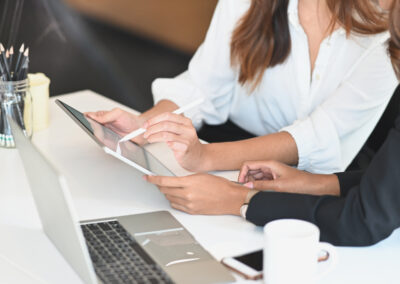
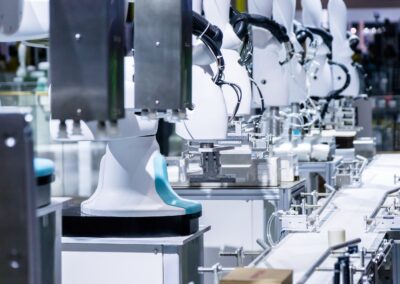
